Case: Schaefer GmbH Automated series production in TIG quality.
The TIG Cobot welds switching panels in the very best quality.
Schaefer GmbH, a specialist for operating and display elements, has been developing and producing system solutions for the lifting industry around the world for more than 55 years. Welding is mainly performed on panels that serve as frames for the various control elements. The basic material is thin sheet metal (V2A), usually 2 mm thick. It is bent, punched, welded, and polished to the order. Since customers pose great demands on looks and clean processing of the weld seams, we use TIG process exclusively.
The company recently started using the TIG version of the new Lorch welding Cobot with great success. The TIG version stands out with its perfectly coordinated overall solution that permits an automated series production of even the smallest batch sizes and in the sensitive TIG area.
Overview of Schaefer GmbH.
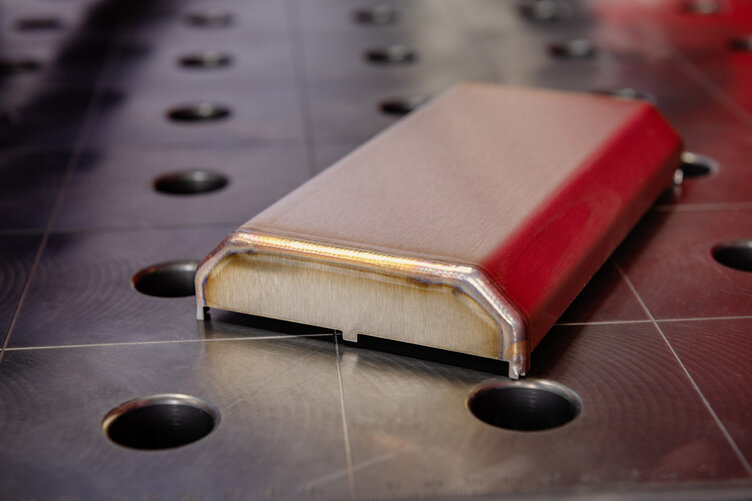
Spatter-free and even weld seams are prerequisites for further processing of the panels at Schäfer.
TIG Cobot versus industrial robot.
The TIG version stands out with its sophisticated features.
The Lorch TIG-Cobot replaces an aged conventional industrial robot at Schäfer. The Cobot solution was not only chosen for its simple operation and the ability to mount the system flexibly on any worktable.
The company was also convinced by the many innovative functions to guarantee efficient and safe processing of tableaus at TIG quality, with an entirely re-designed torch with an ergonomic design that offers a good view of the weld seam and a practical bayonet lock to guarantee a quick torch head change.
A hybrid cooling concept ensures that the torch head does not overheat while welding. This increases the electrode service life while letting the welding torch work perfectly cleanly and reliably.
Highest possible safety during series production.
An installed scanner safety system with audible and visual warning signals and an emergency stop function protect the operator from potential hazards while welding.
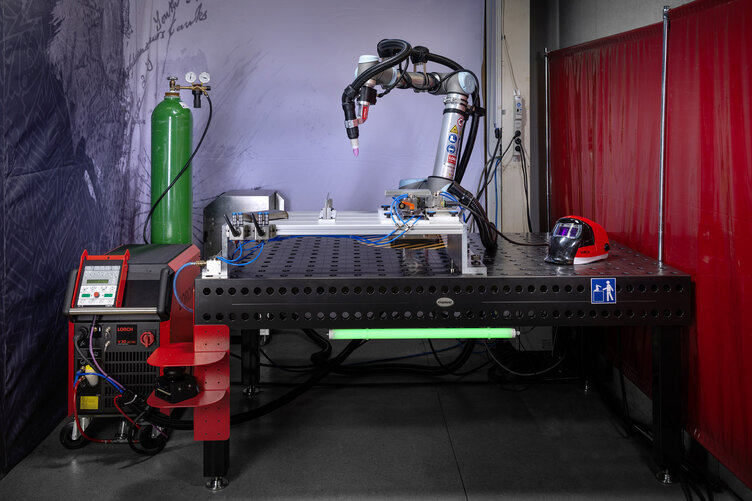
Another benefit is Cobot control.
Cobot control via a free-drive function directly on the torch facilitates guidance of the robot arm, and thereby precise setting on the part. A sophisticated safety system using a laser scanner also ensures the highest possible level of protection for the user while allowing precise parametrisation and setting of the torch directly on the system before starting series production, thanks to activation via an enabling switch in manual mode.
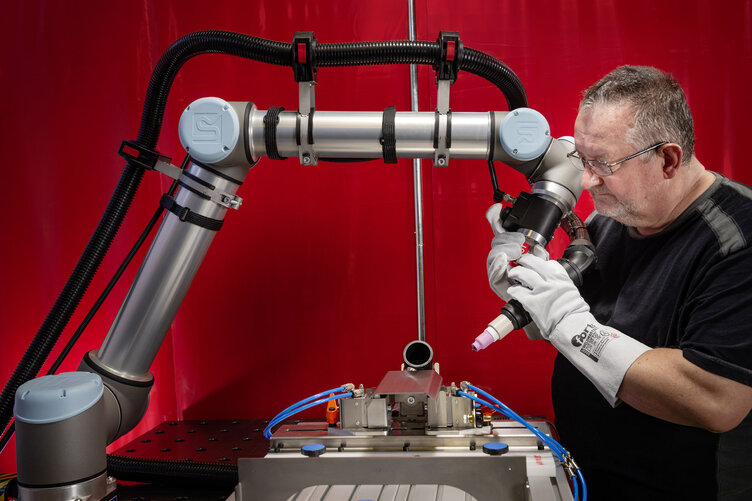
The free-drive function is very easily accessible for the welder right at the torch holder.
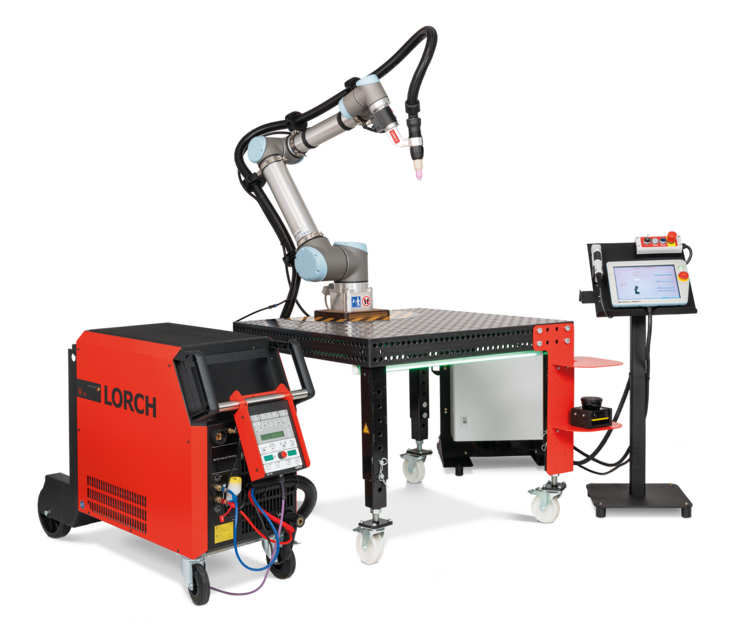
Lorch Cobot Welding Package TIG: Discover it now!
Increase your competitiveness with the Lorch Cobot Welding Package TIG Edition: the easy way to TIG automation.
Cobot welding represents collaborative robot welding in an attractive system for economical welding automation in medium-sized companies. People and robots work hand in hand in a flexible, precise, and efficient manner.
Downloads
Do you want to learn more about the Lorch Cobot Welding Package TIG edition? Technical data as well as further details on application and equipment can be found in the data sheet, and additional information is provided in the brochures: