Case: Dieci s.r.l. Highly efficient welding at best quality thanks to Lorch’s S-series
The Lorch S-series stands out with optimal welding performance
Italian company Dieci is a global market leader for telehandlers. Its powerful all-rounders are developed and built in Montecchio, near Parma, from where they are shipped out to do their hard work around the world.
Overview of Dieci s.r.l.
Precise weld seams under extremely high loads
Dieci was looking for MIG-MAG-welding systems that would allow the company to weld faster while also achieving a higher deposition rate and deeper penetration in order to optimise production of the high-end “Hercules” machines. Dieci welders must complete around 100 weld seams manually, horizontally as well as in the form of vertical up and down welds, and at times in rather tight working conditions, for the 6.6-metre-long and 2.2-metre-wide vehicle frame alone.
Each of these weld seams must fit precisely since they connect steel sheets with a thickness of up to six centimetres. These must withstand extremely high loads in use as the frame alone has a dead weight of 27 tonnes. Enormous forces act on the chassis when the telehandler lifts weights in excess of 14-tonnes as well. Following a comprehensive selection process with several suppliers, Dieci now uses four Lorch S-series systems to weld with high efficiency at the very best quality.
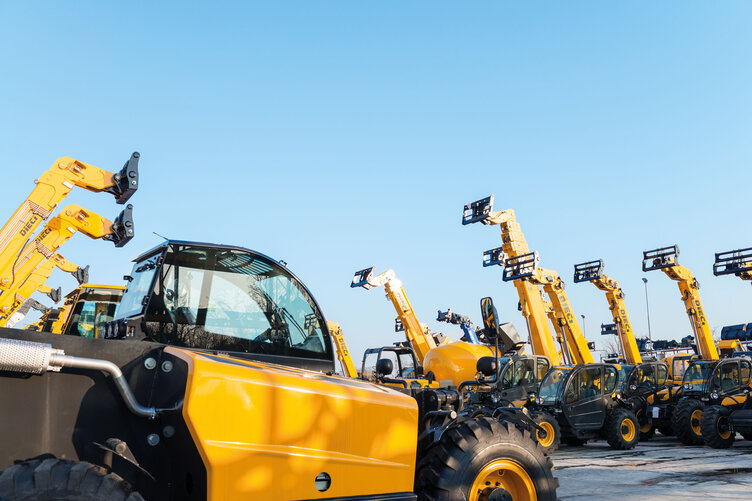
The highest-performance Dieci telescopic wheel loader is used in companies from the construction industry around the world. Extremely high forces act on the chassis of the wheel loader with a maximal transport load of 14 tonnes.
Ideal for large parts:
The welding parameters can be set directly at the torch with the Powermaster remote control.
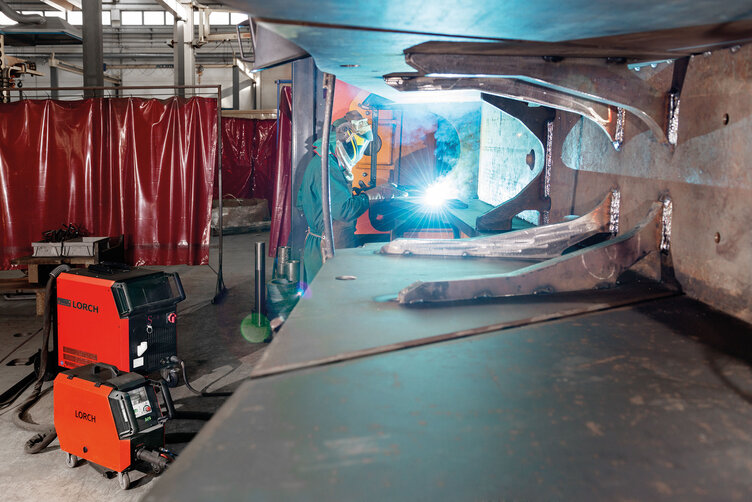
Weld up to 48 percent more quickly with the S-SpeedPulse series.
Less distortion and rework due to lower heat input.
Dieci has been able to significantly increase welding process efficiency by using the S-SpeedPulse series. This is because the patented SpeedPulse process of the S-SpeedPulse series combines the speed advantages of the spray arc with the application and quality advantages of the pulsed arc. As a result, steel and stainless-steel materials can be welded up to 48 percent faster. Additionally, the welder has better control of the arc and the weld pool. All of this is done at consistently high seam quality.
Another advantage of the S-SpeedPulse series is the significantly smaller heat-affected zone. The concentrated arc reduces the heat application to the material considerably by comparison to the other processes. The sheets twist or warp far less, minimising rework. In fact, Dieci now eliminates the need to realign the chassis plates entirely. The direct Powermaster remote control on the torch additionally allows welders to avoid time-consuming paths and reduces their noise exposure with the new welding units since the SpeedPulse is reduced by up to 10 dB (A).
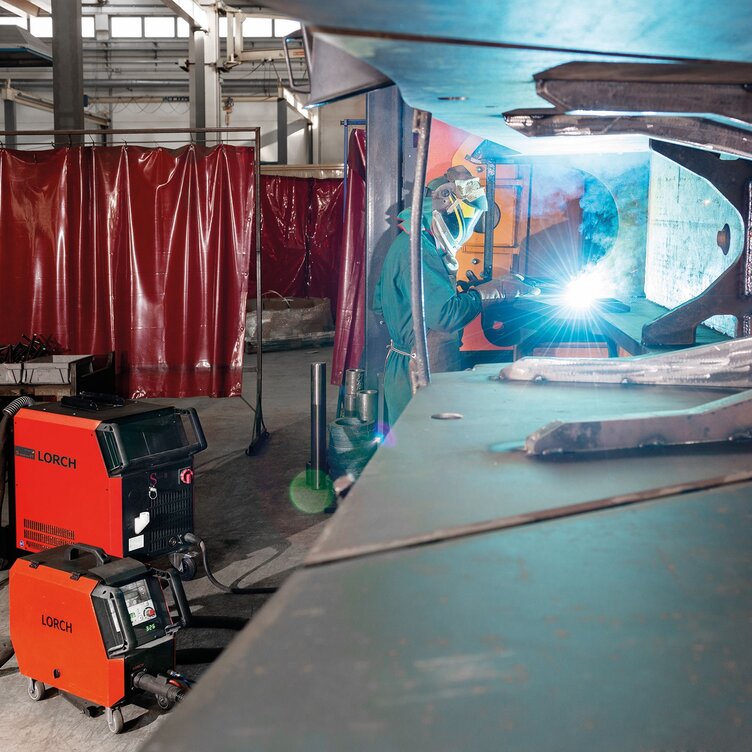
Excellent weld seam surface, deep penetration:
Cross-beams can be optimally welded with only one layer.
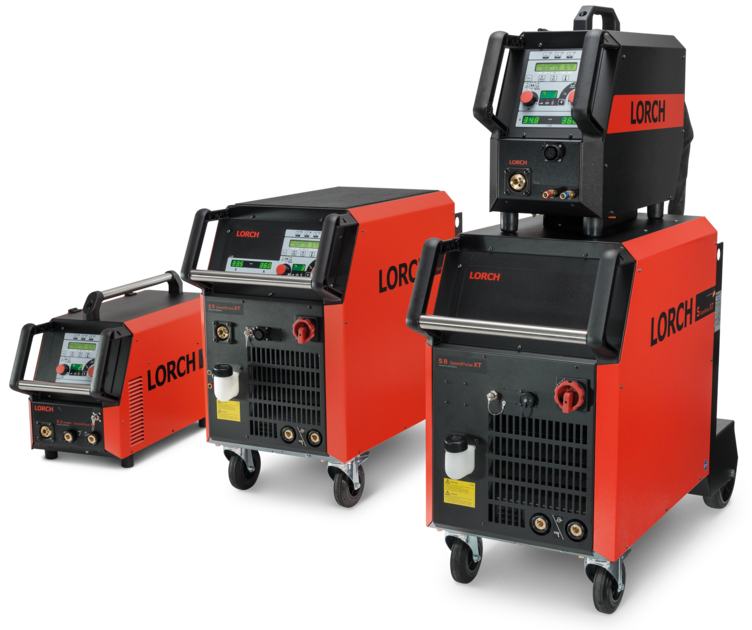
The S-series: Premium MIG-MAG welding units made to measure.
S-series welding units adapt perfectly to your needs, while MIG-MAG Speed processes combine greatest efficiency and quality. Configure the S series precisely to your needs to ensure that your system fits perfectly into the production environment and welding task. On top of this, all S-series welding units are complemented by their intuitive operating concept that provides easy access to all setting options. Learn more now or find a competent Lorch partner near you for personal advice!
Downloads
Do you want to learn more about the Lorch S-series? Technical data as well as further details on application and equipment can be found in the data sheet, and additional information is provided in the brochures: