Case: ADK d.o.o Save production time with the Lorch SpeedPulse process and S-series.
Extensive preparation and rework are not required.
ADK d.o.o. was founded in 1995. It has grown into one of the most successful Slovenian companies in the steel construction industry. ADK manufactures machines and equipment of high-strength steel for lifting heavy loads as well as large-scale equipment for raw material extraction and for the construction industry in its four sites. Virtually everything in ADK’s production revolves around welding, with about 160 welders working at the Hoče site alone.
Overview of ADK d.o.o.
Standard-compliant welding poses the highest demands on welding unit and welder.
Welding is performed exclusively in accordance with DIN EN ISO 5817, the reference standard for the quality assessment of weld seams. Previously, ADK had to perform plenty of time-consuming additional grinding and gouging to meet these requirements. Converting the machine park to the Lorch S series with the SpeedPulse process has enabled ADK to eliminate the time-consuming and expensive preparation and rework while ensuring optimal weld seam quality with deep penetration.
The SpeedPulse advantage:
Faster welding due to smooth material transition.
The SpeedPulse welding process combines the speed advantages of the spray arc with the advantages of the pulsed arc. The qualities of a good pulse arc are known to be the virtually spatter-free, ideal weld-pool control, controlled material transfer, and virtually no rework requirements. What exactly increases speed as compared to a standard pulse process, however? Before, each pulse equalled one drop. The Lorch process specialists found a way to extend this drop and allow a controlled, virtually flowing material transition to the workpiece. A pulsed guiding drop is always followed by a second one, which leads to a specifically controlled, spray-arc-like material transition. This extra material clearly increases speed as compared to a standard pulse, while maintaining the best pulse quality and improving handling by far.
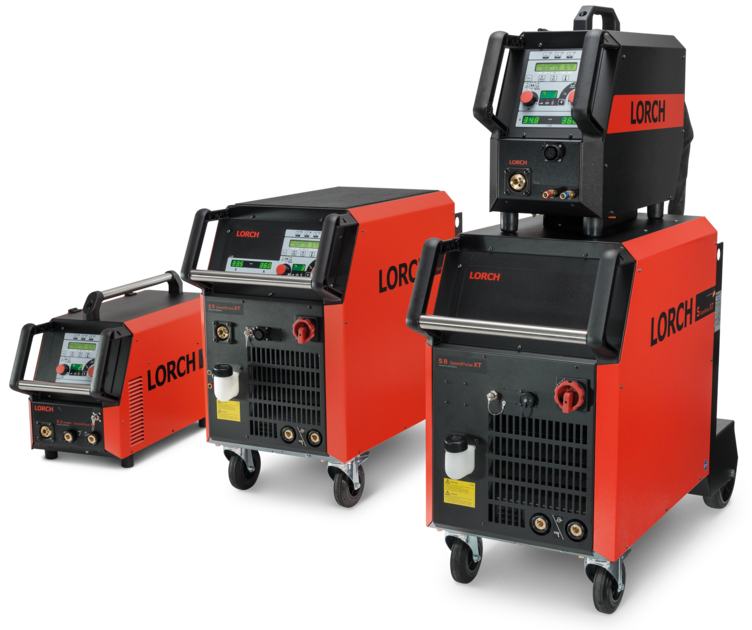
The S-series: Premium MIG-MAG welding units made to measure.
S-series welding units adapt perfectly to your needs, while MIG-MAG Speed processes combine greatest efficiency and quality. Configure the S series precisely to your needs to ensure that your system fits perfectly into the production environment and welding task. On top of this, all S-series welding units are complemented by their intuitive operating concept that provides easy access to all setting options. Learn more now or find a competent Lorch partner near you for personal advice!
Downloads
Do you want to learn more about the Lorch S-series? Technical data as well as further details on application and equipment can be found in the data sheet, and additional information is provided in the brochures: