Case: Rösler Oberflächentechnik GmbH Production time reduced by 50 percent, competitiveness significantly increased.
THE SWITCH FROM MANUAL WELDING TO THE LORCH WELDING COBOT HAS PAID OFF PERFECTLY FOR RÖSLER.
Rösler Oberflächentechnik GmbH is a global market leader in the production of vibratory finishing and shot blasting equipment. With its 1700 employees, it represents the highest manufacturing quality. The company offers excellent solutions for treatment of component surfaces on anything from small crank rods to 20-metrelong workpieces. The core elements are turbines that feed the blasting material into the chambers in the field of blasting technology. The company applies the Cobot Welding Package from Lorch with great success in the demanding production of manganese steel turbine housings. The alloyed high-performance steel is very difficult to weld. The sheets used, which are eight to ten millimetres thick, warp quickly, and there’s plenty of spatter, too. Therefore, the time required for post-processing of the workpieces was very high for these parts. The cobot helps the company cut production time per turbine in half while benefiting from easy reproducibility of high-quality weld seams. Rösler’s investment in the cobot has almost completely paid off already after only 10 months.
Overview of Rösler Oberflächentechnik GmbH.
Quick integration into work flows due to simple operation.
THE COBOT NOW ALSO WELDS MANGANESE STEEL WITHOUT PROBLEMS.
The welding cobot was quickly integrated into Rösler’s work processes. Thanks to its user-friendly operation, it could be used after only two days of training and is now operated in two shifts by a total of four welders. The system is placed between two work tables and all weld seams of the turbine housing can now be welded fully automatically in three set-ups. Once the weld seam has been precisely programmed and stored, the cobot also reproduces the weld seams in the highest quality on other parts. The cobot also impeccably completes the challenging circumferential weld seam on the outer turbine chassis. Optimal torch guidance and finely tuned adjustment of the welding parameters allows much better control of manganese steel, which is difficult in terms of “tensile stress”. Time-consuming straightening of the workpieces is eliminated entirely.
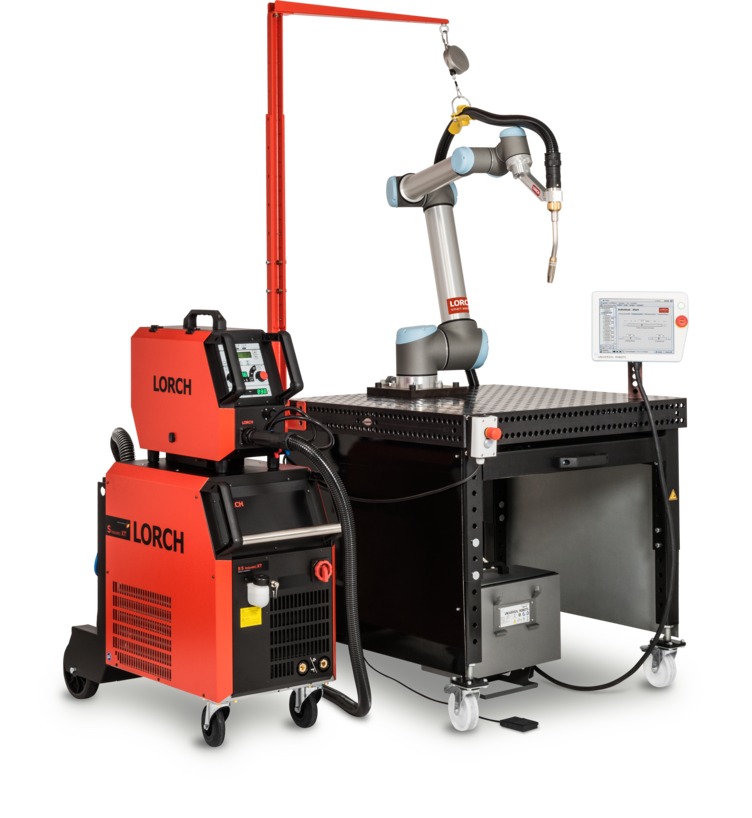
The Lorch Cobot Welding Package MIG-MAG: Get going now!
Cobot welding means collaborative robot welding for medium-sized companies. The MIG-MAG edition of the Lorch Cobot Welding Package is the ideal tool for economical welding automation in small and medium series production. What are you waiting for? The Lorch Welding Package MIG-MAG lets you start automating your welding production right away.
Downloads
Do you want to learn more about the Lorch Cobot Welding Package MIG-MAG? Technical data as well as further details on application and equipment can be found in the data sheet, and additional information is provided in the brochures: