Case: Resch Maschinenbau GmbH Productive from day two onwards with the Cobot.
Variable production and cost-efficient welding of even the smallest series.
Acquisition of the welding Cobot by Resch Maschinenbau GmbH was facilitated by a major order from a leading professional document management provider, too large to be completed without hiring additional welders, who are hard to find on the job market at this time or switching to automated welding technology.
The Lorch welding Cobot now allows welding of workpieces from a throat thickness a of three millimetres onwards automatically with the MIG/MAG process. The Cobot can fully play its advantages even at small quantities.
Overview of Resch Maschinenbau GmbH.
Cobots - fast and flexible:
The fast and flexible welding Cobots pay off for Resch starting at a quantity of 4-5 workpieces.
The welding process is "programmed" via the touch display. Alternatively, the torch is moved to the start and end position by hand using the free-drive function.
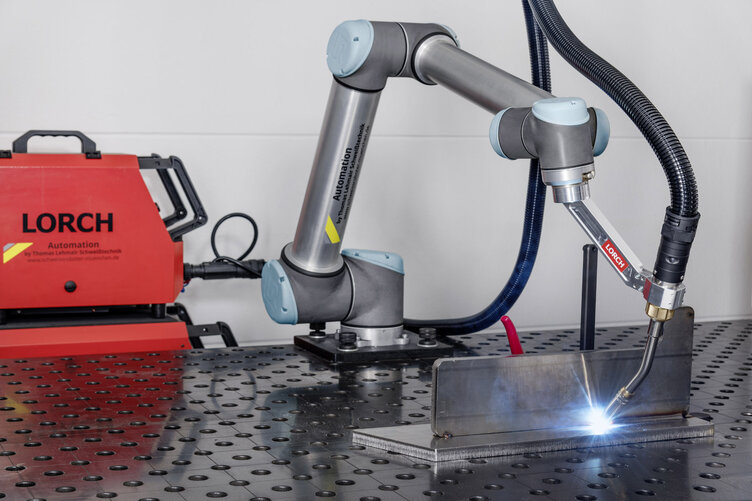
Rendering production more flexible.
The Lorch Cobot Welding Package offers clear advantages in welding as well as by adding variability throughout the production process. Once a welding project has been programmed, repeat parts can be added to the production sequence at short notice at any time.
Less distortion and significantly less rework:
TwinPuls XT as the decisive process for the changeover.
A traditional robot was also considered for the system. However, not only were the investment costs for a Lorch Cobot significantly lower, but so was the programming effort. The Cobot also can be set up easily at any workplace since no separate safety enclosure is required.
Resch Maschinenbau is currently trying to convert various TIG projects to the MIG/MAG process. Resch Maschinenbau still has to convince its customers of this, as they often want to stick to the TIG welding process for traditional reasons. Lorch offers the decisive procedure for the changeover with the TwinPuls XT welding process. The welding process controls the heating and cooling phases separately in a targeted manner, ensuring a significantly lower and more targeted heat input into the workpiece, and as a result much less distortion and significantly lower rework needs, rendering welding much faster and more efficient.
Perfect introduction.
Productive welding with the Lorch Cobot started on the second day already.
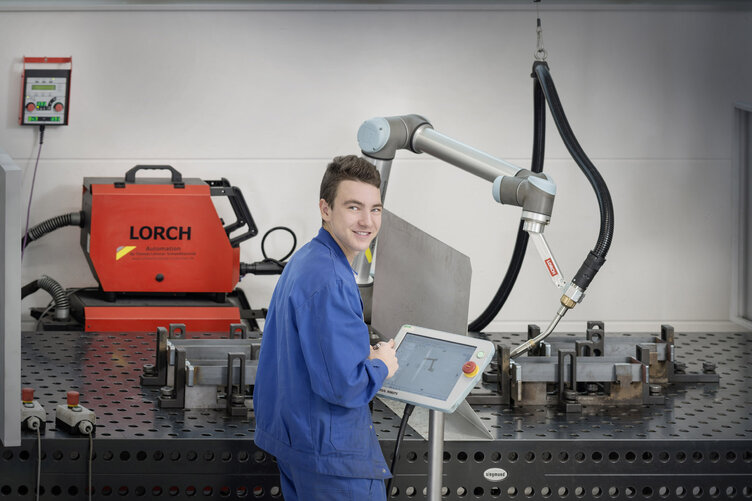
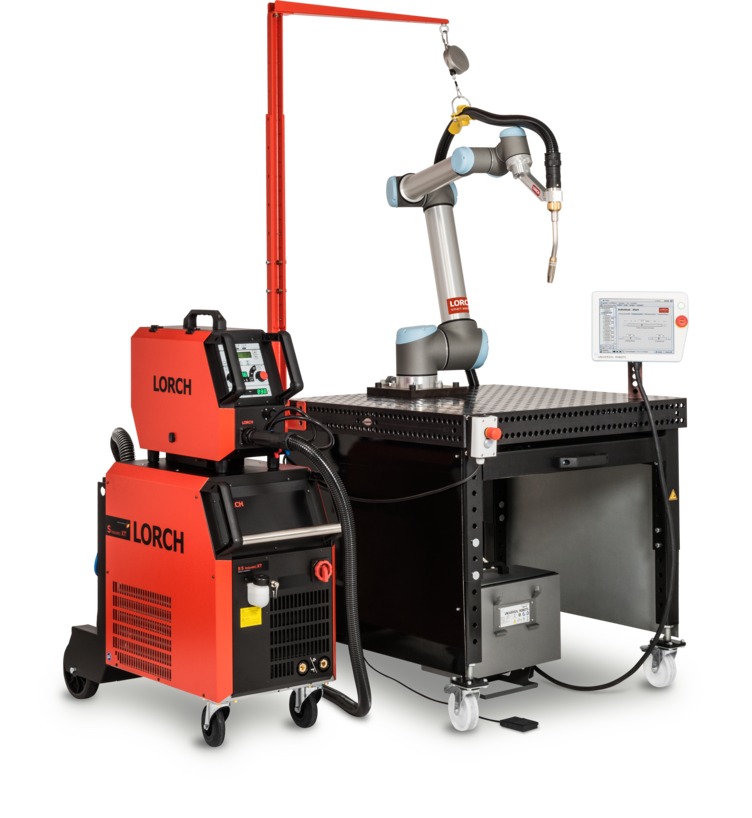
The Lorch Cobot Welding Package MIG-MAG: Get going now!
Cobot welding means collaborative robot welding for medium-sized companies. The MIG-MAG edition of the Lorch Cobot Welding Package is the ideal tool for economical welding automation in small and medium series production. What are you waiting for? The Lorch Welding Package MIG-MAG lets you start automating your welding production right away.
Downloads
Do you want to learn more about the Lorch Cobot Welding Package MIG-MAG? Technical data as well as further details on application and equipment can be found in the data sheet, and additional information is provided in the brochures: