Case: GOH Behälter- und Anlagenbau GmbH Three times faster welding with the Lorch SpeedRoot and SpeedPulse processes.
Highest demands in tank and pipeline construction.
GOH Behälter & Anlagenbau GmbH produces high-quality vessels and piping components for plant manufacturers, leading compressed-air-processing companies, the chemical and aviation industries. Made of stainless steel and carbon steel at a sheet thickness of up to 120 mm, vessels must withstand pressures of up to 1,000 bar. This poses an enormous challenge to the quality of each individual weld seam, in particular since an optimal weld pattern is indispensable.
Overview of GOH Behälter- und Anlagenbau GmbH.
Welding becomes more efficient by switching from TIG to MIG-MAG:
Root weld seams in the round profiles processed at GOH used to be welded using TIG, which allows joining of the material with a greatly non-porous structure. However, it has the disadvantage of being a very slow welding process.
The vessel manufacturer from Siegerland is now not only welding spatter- and pore-free, but also up to three times more quickly after switching to MIG-MAG-welding in combination with the Lorch SpeedRoot and SpeedPulse procedures.
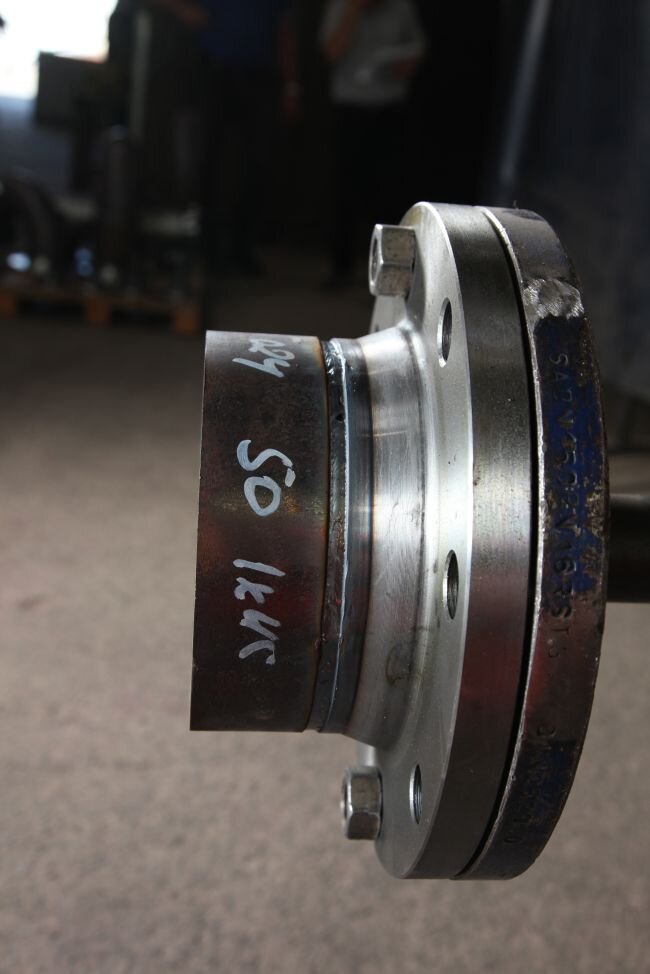
Fast and clean root welding with the Lorch SpeedProcesses
Spatter-free and with very low energy input, SpeedRoot closes even eight-millimetre gaps in root welding three times faster than TIG processes.
Pressure vessels around the world.
GOH’s high-quality pressure vessels can be found, among other things, in air-treatment plants, filter systems for aircraft refuelling systems, or as CO2 generators for the beverage industry.
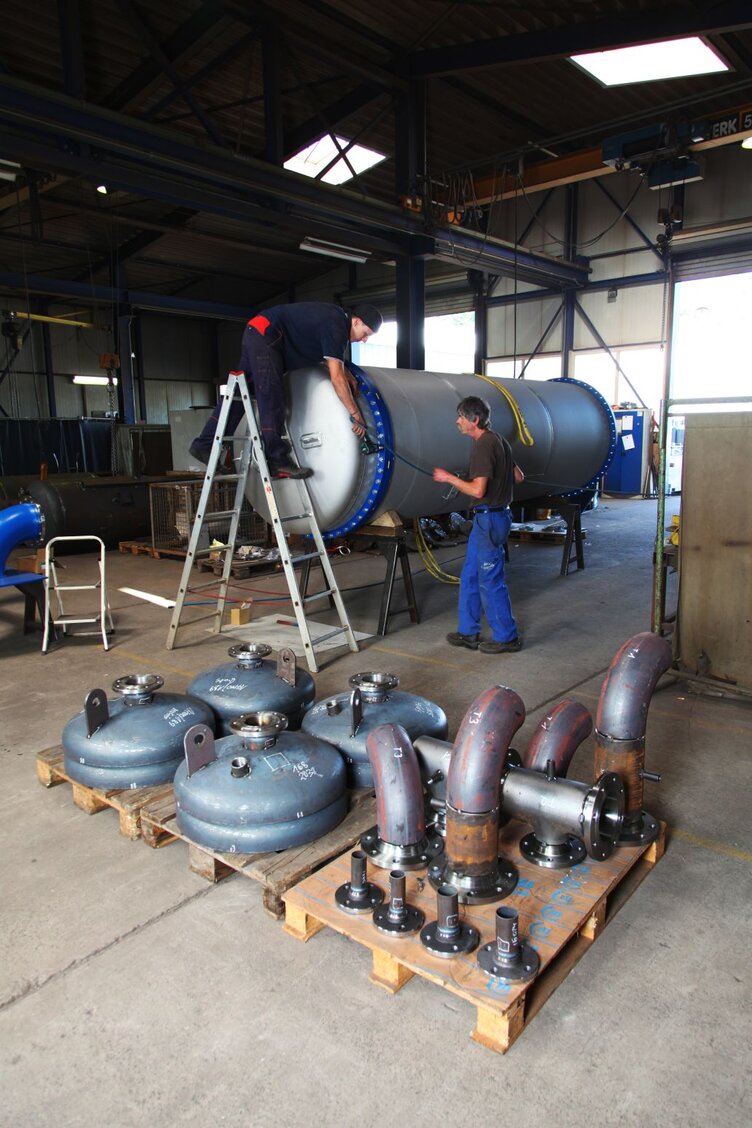
The advantages of MIG-MAG-welding systems, combined with SpeedRoot and SpeedPulse:
Shorter welding times, deep penetration
SpeedRoot is a MIG-MAG process based on the S-SpeedPulse welding systems that combines a TIG-like root weld quality with the MIG-MAG speed advantages. Welding a root layer on a pipe socket that used to take 12 minutes with TIG now takes the company only eight minutes anymore. On top of this, where up to three welding units were needed for the various weld seam layers with several wires and gas mixtures in the past, GOH now handles this with a single SpeedPulse system. The switch between solid and flux-cored wire is also almost no work at all succeeds anymore due to the double-wire feeder and without gas escaping.
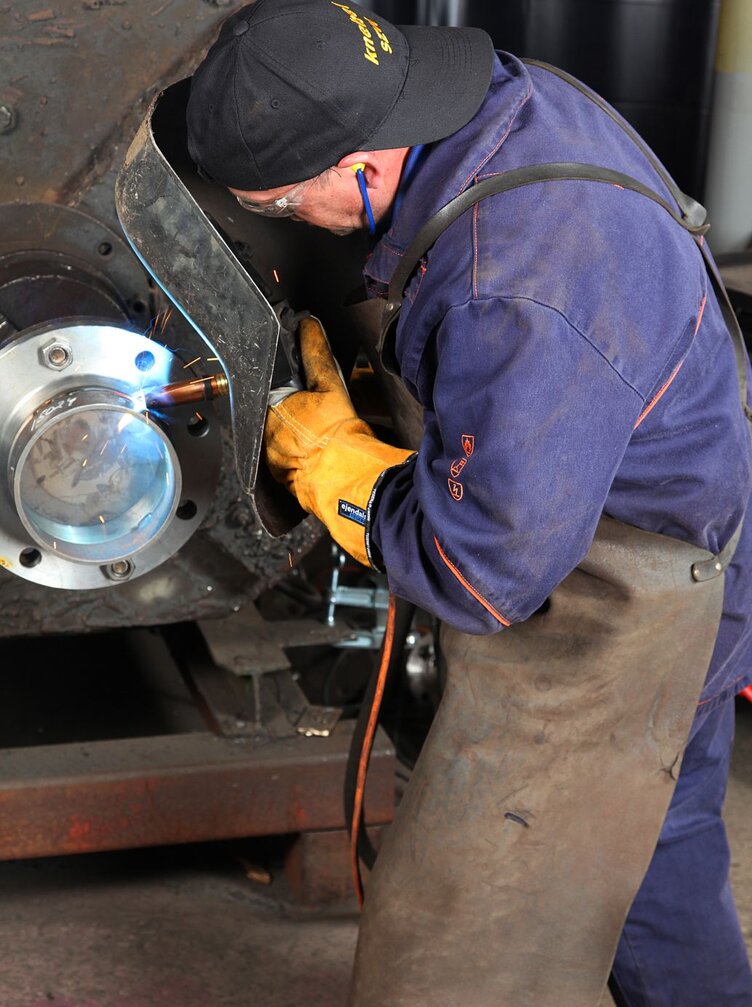
Combining both processes offers the optimal solution for GOH’s welding tasks
Luis Braga welds the root layer of the pipe socket with a Lorch S-SpeedPulse machine using Lorch’s SpeedRoot process. The top layer is welded with Lorch SpeedPulse.
Easily bridging gap widths
Since the root is grasped safely and deeply, the welders at GOH can now even avoid the trouble of welding a counter-pass since SpeedPulse ensures a smooth material transition to the workpiece. In the course of this, a pulsed guide drop is always followed by a second, specifically controlled, spray-arc-like material transition, making it possible to bridge gap widths of up to 10 mm without any problems at all and, in the case of solid ball resonators, filling even a penetration depth of 120 mm with a single weld seam. All in all, the welding process only takes one third of the time like this.
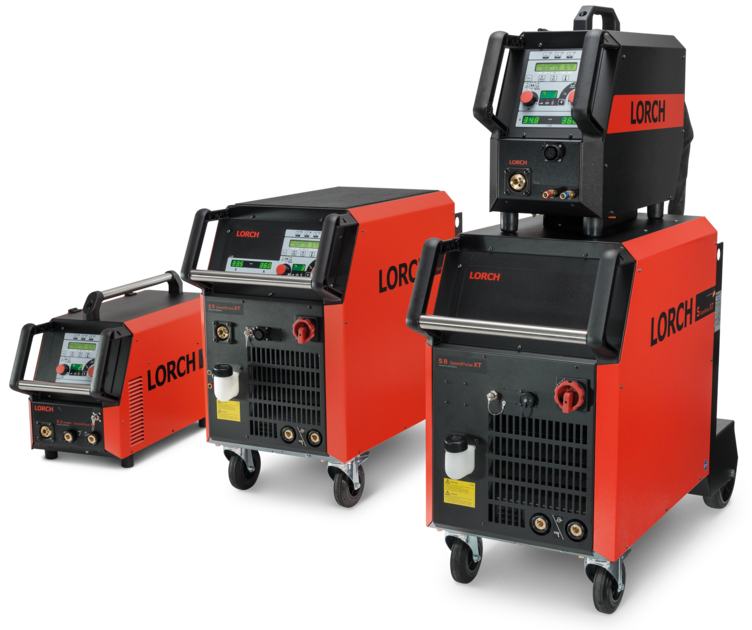
The S-series: Premium MIG-MAG welding units made to measure.
S-series welding units adapt perfectly to your needs, while MIG-MAG Speed processes combine greatest efficiency and quality. Configure the S series precisely to your needs to ensure that your system fits perfectly into the production environment and welding task. On top of this, all S-series welding units are complemented by their intuitive operating concept that provides easy access to all setting options. Learn more now or find a competent Lorch partner near you for personal advice!
Downloads
Do you want to learn more about the Lorch S-series? Technical data as well as further details on application and equipment can be found in the data sheet, and additional information is provided in the brochures: