Case: Maschinenbau Manfred Kaiser GmbH Power welding in continuous operation with P-series welding units.
The ideal welding unit for companies with a high weld performance.
Started in 1987 in the owner’s garage in Vrees, Manfred Kaiser Maschinenbau GmbH has grown into a leading specialist supplier of construction machinery, counting more than 100 employees. From the mini bucket of the excavator to the 12-cubic-metre swimming-pool-sized rock bucket of a wheel loader, this specialist manufactures anything that gets construction machinery ready for special applications. Depending on the size, add-on parts are custom-welded from steel sheets at thicknesses from eight to 200 mm.
Overview of Manfred Kaiser Maschinenbau GmbH.
Lorch is the logical choice for extreme demands to the weld seam at extreme working conditions.
Maximum priority: Any weld seam, no matter if in regular structural steel, special material such as Hardox 450, 500 or fine-grained structural steel up to S 700 QL, must be placed perfectly to withstand the extreme loads these tools are subject to.
The company sends out more than 1200 parts every year. Enquiry and delivery are often merely a week apart. The welding units run continuously under high load (340-350 amps) in order to reliably maintain such short reaction times.
The company chose Lorch equipment for modernising its machinery, following a thorough test procedure that compared several suppliers. They invested in 60 new welding units of the powerful P 5500 series.
Why? Lorch systems deliver the highest weld seam quality, the longest service life at the lowest possible energy consumption as well as best welding performance even in constrained positions.
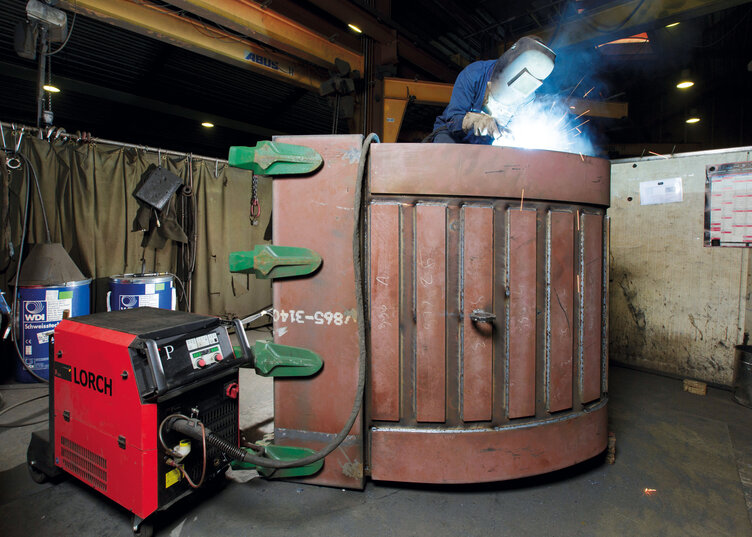
Power welding in continuous operation with P-series by Lorch.
Permanently at work around the clock: The P-series provides full performance under extreme conditions. Manfred Kaiser Maschinenbau GmbH works at 15 welding stations, day and night. Luckily, the P-series welding units are particularly energy-efficient to keep costs under control.
Up to 50 percent productivity increase.
Parts often require in excess of 100 weld seams per piece. Some of them have 14 to 16 connection layers and extremely thick materials. Lorch’s MIG-MAG speed processes can increase productivity by up to 50 percent, in particular to meet challenges such as faster welding and less rework.
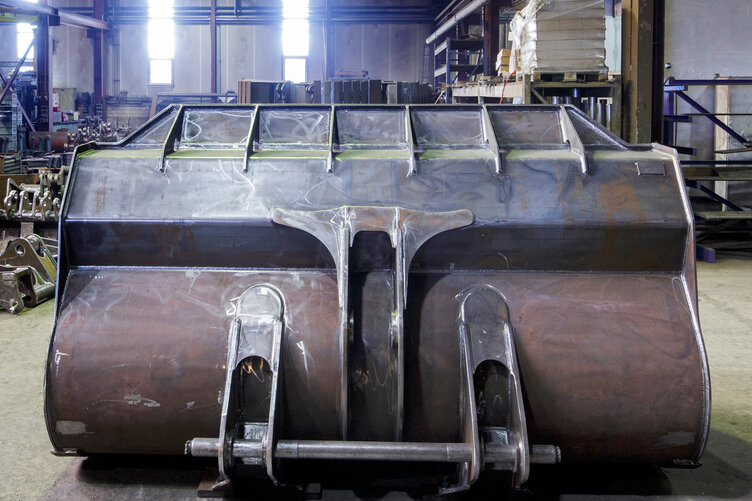
Innovative inverter technology combined with highly efficient MIG-MAG welding processes.
Faster and more economical welding with SpeedArc.
Saprom inverter technology, combined with highly efficient MIG-MAG welding processes such as SpeedArc, keeps energy consumption at Kaiser down by a considerable margin. The clearly focused arc gives SpeedArc a higher power density than other welding processes, raising the arc pressure point in the weld pool to significantly reduce operating costs.
This has the advantage of making weld seam completion faster by up to 30 percent and allowing even thicker steel sheets to be welded in a single layer with the SpeedArc. This may save as much as 50 percent of the production time in weld seams that may have 14 to 16 connection layers. While welding speed increases, the rework requirements drop.
Innovative inverter technology combined with highly efficient welding processes.
Faster and more comfortable welding with SpeedUp.
Kaiser was also able to significantly increase its productivity in repairs. Many parts must be welded in constrained position with vertical welds due to their sizes and weights. SpeedUp dispenses with the time-consuming “X-mas tree technique”, allowing the welder to simply pull the weld seam straight up for an enormous speed advantage and guaranteeing the optimal root layer for the welder.
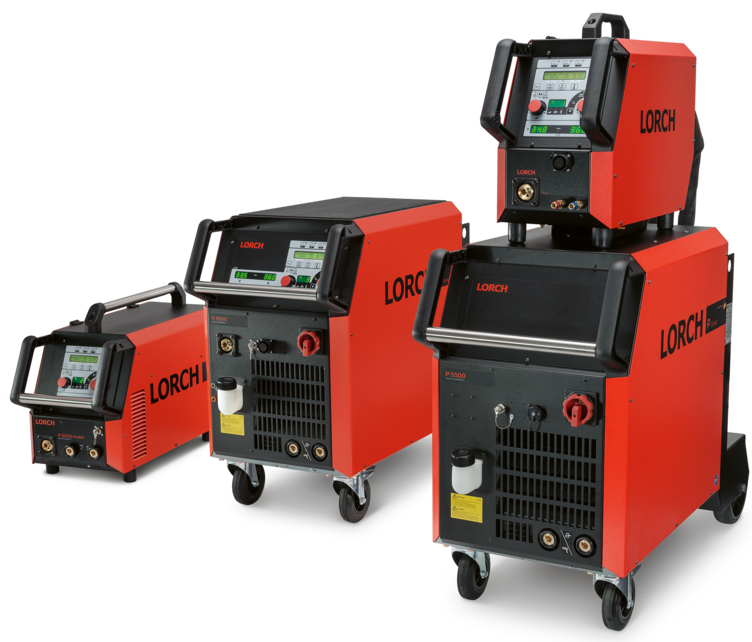
The P-series offers energy-efficient top performance around the clock.
P-series welding units offer everything MIG-MAG-welding in shift operation needs: Performance, duty cycle, reliability. Configure the P series precisely to your needs to ensure that your system fits perfectly into your production environment and your specific welding task. Learn more now or find a competent Lorch partner near you for personal advice!
Downloads
Do you want to learn more about the Lorch P-series? Technical data as well as further details on application and equipment can be found in the data sheet, and additional information is provided in the brochures: