Case: Steelflex High flexibility, efficiency, and benefits from digitalisation.
Steelflex continues on its growth course with 21 new welding systems by Lorch.
Steelflex S.r.l., headquartered in Pioltello, in the Milan region, is a leading manufacturer of stainless-steel and special-alloy expansion vessels. Founded in 1978, the company has acquired a global reputation where compensation of thermal and mechanical expansion of pipes using expansion elements is concerned since. Steelflex is employing more than 70 employees today, acting as the solution partner in many industry sectors, such as pharmaceutics, petrochemistry, steel and ship construction, or the food industry. Within the scope of a comprehensive future-oriented project, the company invested in a fleet of 21 new welding systems by Lorch. Using the S-XT-series as well as the V- and T-series units, Steelflex is now able to not only clearly reduce its welding times while further increasing the quality of its weld seams but also profits from the diverse options of the systems and the ability of digitising the welding processes.
Overview of Steelflex S.R.L.
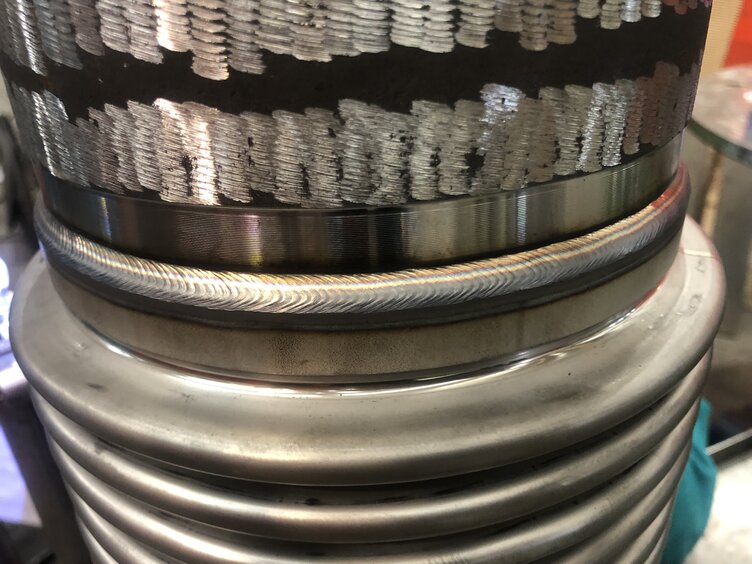
Top priority:
Precise weld seams and low material distortion enjoy the highest priority in production of the complex expansion elements (expansion vessels).
V-series, T-series, S-series with SpeedPulse-XT, Lorch Connect
Specific requirements are optimally met.
The new welding unit fleet is perfectly adjusted to the production requirements at Steelflex. The Lorch Feed TIG cold wire feeder of the V-series allows welding with controlled and continuous material supply without having to interrupt the welding process. The entire welding process is digitally controlled and takes place in the highest precision, as well as including the option of synchronising the wire feed with the pulse function, saving time when welding and getting rid of the elaborate wire change. The mobile T-series welding units are characterised not only by outstanding TIG welding properties. The integrated SmartBase parameter database by Lorch also provides precisely the right parameters for an optimal arc for each alloy. The S-series and the SpeedPulse-XT welding process has clearly shortened the production times for MIG-MAG welding at Steelflex. The patented XT control technology enables the company to not only achieve much higher welding speeds, but also clearly reduces the thermal distortion of the parts and makes the welding process as such much lower-spatter. Thanks to Lorch Connect, the company can save and analyse all production data and can keep data on costs, wire and gas consumption calculations, or usage hours precisely in view in real time.
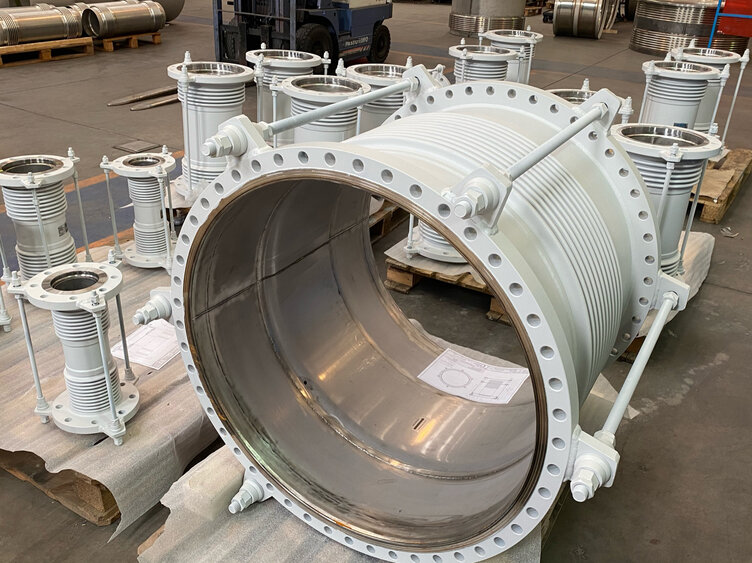
Indispensable in plant engineering: Expansion vessels
compensate for the thermal and mechanical changes to the pipes. They need to be perfectly tight while remaining flexible. They can be as much as two metres in diameter.