Case: Pladdet More efficient welding, optimised inventories, shorter delivery times.
Pladdet is relying on automated welding technology by Lorch and Yaskawa.
Pladdet, headquartered in Zealand-Flemish Biervliet in the Netherlands, specialises in the production and delivery of high-quality construction machines and attachments. Founded more than 80 years ago, it has grown into an internationally active company with more than 100 employees and a broad network of representatives and dealers in and outside of the country, exporting its high-quality products world-wide. The company is welding attachments in small and medium batch sizes much more quickly and efficiently and can process even large parts such as entire excavator buckets that had to be welded manually before, with the introduction of automated welding technology, a Lorch Cobot Welding Solution, and a robot installation by Lorch and Yaskawa. This allows faster topping up of stocks and shortening of delivery times.
Overview of Pladdet B.V.
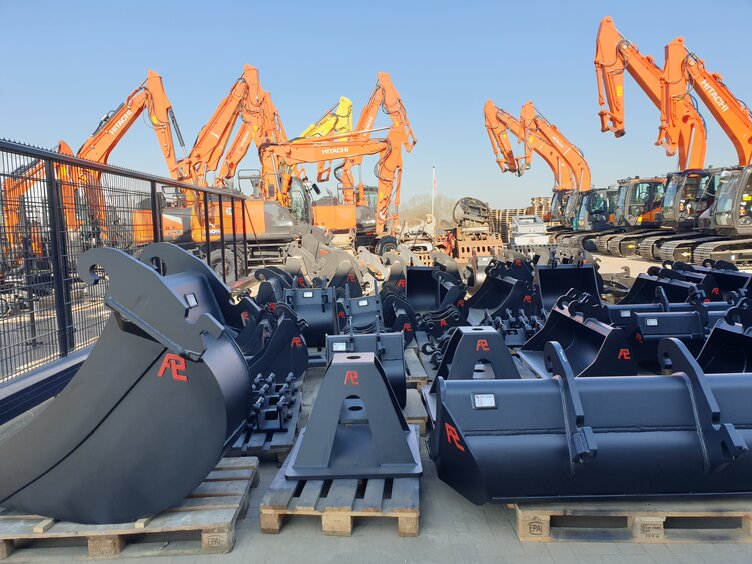
Globally active specialist for construction machinery:
Founded more than 80 years ago, Pladdet B.V. is now producing highquality equipment for excavators and wheel loaders.
Lorch Cobot Welding Solutions and robot installation by Lorch and Yaskawa.
Two automation solutions that ideally supplement each other at Pladdet.
The Cobot has many advantages in particular for smaller attachments that are often welded in batch sizes of 20 to 30 at Pladdet. With the option of saving the welding processes for each part, a weld seam can be reproduced with the Cobot as often as desired. Once the parameters and welding process have been optimised for a part, the weld seam produced by the Cobot warrants a consistently high quality. Time-consuming rework can be minimised to gain valuable time and avoid rejects even during production of small batches. The robot system designed by Lorch and Yaskawa is ideal for efficient welding of larger and more complex workpieces: It comprises a Yaskawa Motoman welding robot with a reach of 2010 millimetres and a payload of 12 kilograms, two Yaskawa manipulators, and the S8 RoboMIG XT power source by Lorch. The entire system is designed for two workstations separated from each other by a glare protection. A freely programmable running rail with a length of 9,150 millimetres connects the welding robot to the two workstations, permitting flexible use on either side. Advantage: While the robot is welding reliably on one side, another workpiece can already be prepared for welding on the other one.
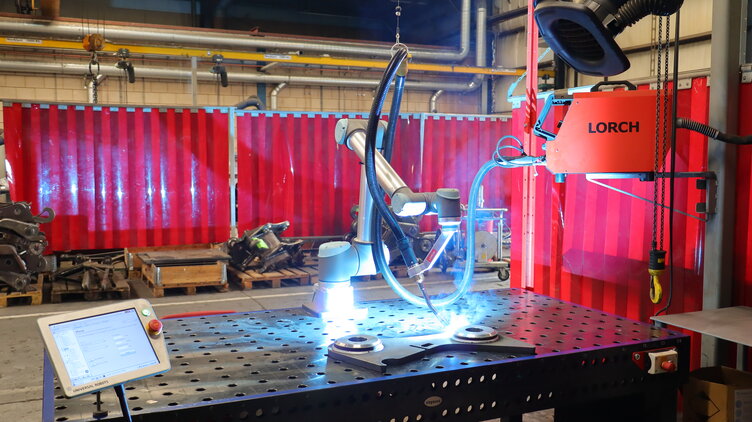
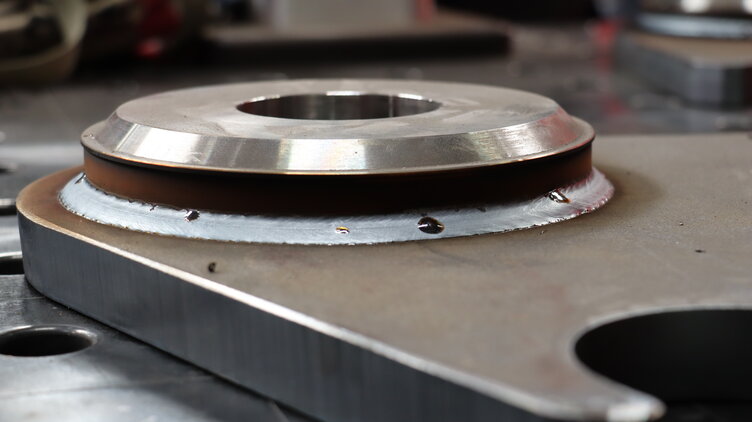
Ideal for small parts such as quick exchange systems: Lorch Cobot Welding Solutions.
The welding Cobot by Lorch
warrants finest MIG/MAG weld
seams in high quality at all times.
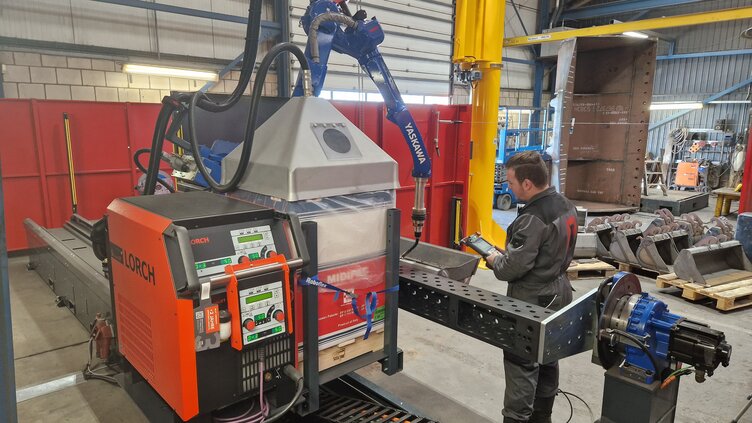
"The robot installation by Lorch and Yaskawa is our perfect supplement for the Cobot. We can use it to weld heavier and more complex workpieces that needed to be welded manually before more quickly and reliably with it as well."
- Alko van Gils -